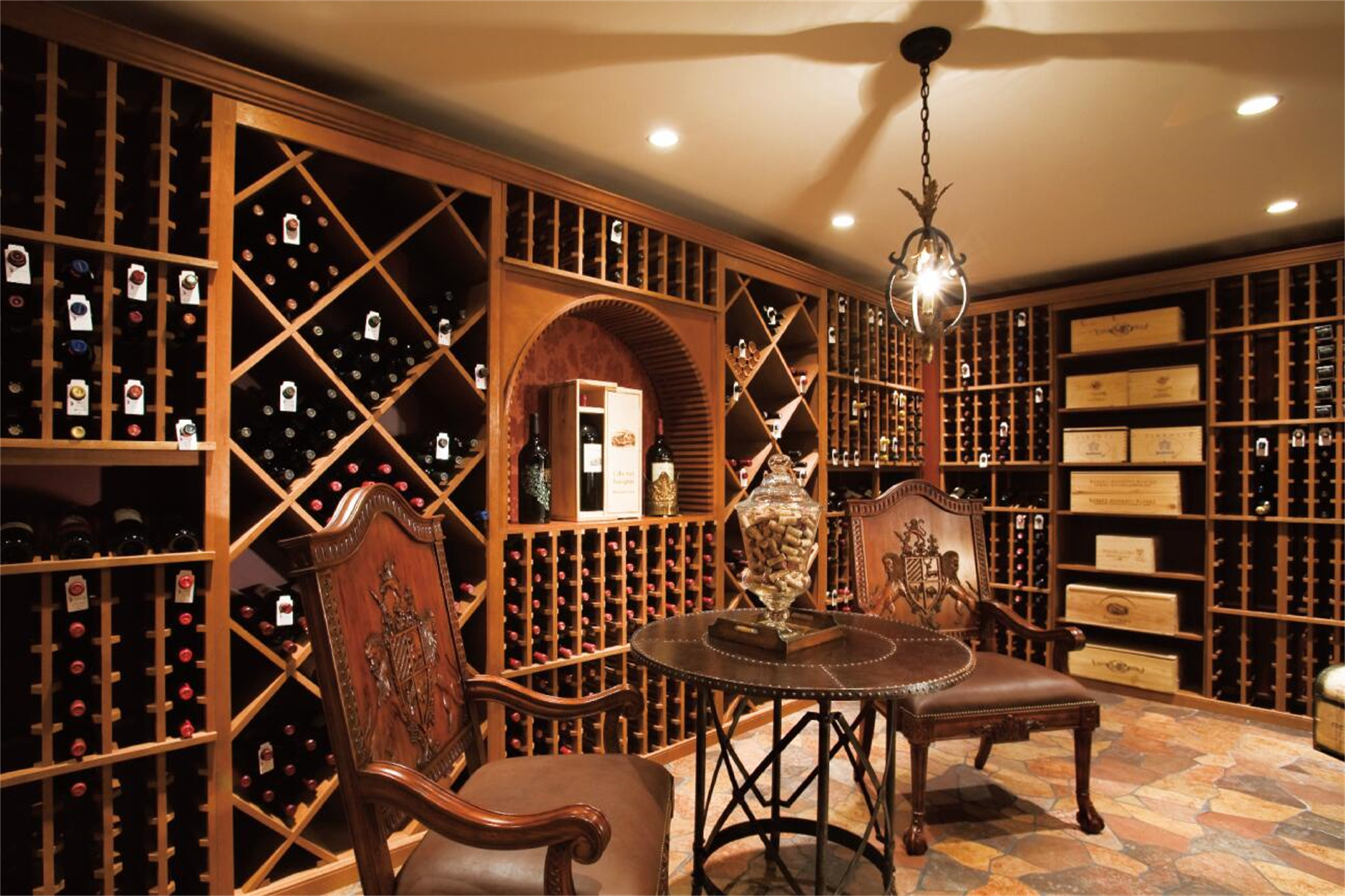
1. Introduction
Acrylic resins, derived from the polymerization of acrylic and methacrylic monomers, have revolutionized industries reliant on reliable bonding, coating, and sealing solutions. Their popularity stems from a unique combination of properties: chemical resistance, weatherability, optical clarity, and, most notably, the ability to tailor tack, adhesion, and strength through precise formulation. These three properties are foundational to their functionality: tack enables initial bonding, adhesion ensures long-term substrate attachment, and strength prevents cohesive failure under stress.
In applications ranging from medical tapes to automotive adhesives, the balance between tack, adhesion, and strength is critical. For example, pressure-sensitive adhesives (PSAs) require high tack for instant bonding, sufficient adhesion to withstand handling, and moderate strength to allow clean removal. In contrast, structural adhesives demand exceptional adhesion and strength with minimal tack during application. This article explores the scientific principles and technological advancements that underpin the control of tack, adhesion, and strength in acrylic resins, offering insights into formulation strategies and practical applications.
2. Fundamentals of Acrylic Resins: Structure and Properties
Acrylic resins are typically copolymers synthesized from monomers such as acrylic acid, methyl methacrylate (MMA), butyl acrylate (BA), and 2-ethylhexyl acrylate (2-EHA). Their chemical structure—characterized by a carbon-carbon backbone with pendant functional groups (e.g., ester, carboxyl, hydroxyl)—dictates their performance. The backbone provides mechanical stability, while pendant groups influence interactions with substrates and other materials.
Monomer Diversity:
Monomers are selected based on their alkyl chain length, polarity, and functionality. For instance, long-chain acrylates (e.g., 2-EHA) enhance flexibility and tack, while MMA contributes rigidity and strength. Polar monomers like acrylic acid introduce hydrogen-bonding capabilities, boosting adhesion to polar substrates (e.g., metals, glass).
Molecular Weight and Distribution: Higher molecular weights generally increase cohesive strength but reduce tack, while lower molecular weights enhance tack but may compromise durability. Narrow molecular weight distributions improve consistency in performance.
Cross-Linking:
Controlled cross-linking via monomers like ethylene glycol dimethacrylate (EGDMA) or post-polymerization treatments increases strength and heat resistance but can reduce tack and flexibility.
These structural variables form the basis for tuning tack, adhesion, and strength, making acrylic resins highly adaptable to specific application needs.
3. Tack: Mechanisms and Modulation
Tack is the immediate, short-range adhesiveness of a material—its ability to form a temporary bond upon light contact with a substrate. In acrylic resins, tack is primarily governed by viscoelastic behavior and surface energy, with formulation and processing parameters playing key roles.
3.1 Mechanisms of Tack
Tack arises from the resin’s ability to flow and conform to a substrate’s surface irregularities at room temperature, maximizing contact area. This process is influenced by:
Viscoelasticity: Acrylic resins with low glass transition temperatures (Tg) exhibit high chain mobility, allowing rapid wetting of substrates. For example, copolymers rich in 2-EHA (Tg ≈ -50°C) flow readily, enhancing tack.
Surface Energy: Resins with surface energy matching or slightly exceeding that of the substrate promote intermolecular interactions (e.g., van der Waals forces), facilitating initial bonding.
Molecular Weight: Low to moderate molecular weights reduce viscosity, enabling better surface wetting and higher tack. However, excessively low molecular weights can lead to excessive flow and poor cohesion.
3.2 Tuning Tack in Acrylic Resins
Formulation strategies to optimize tack include:
Monomer Selection: Increasing the proportion of flexible monomers (e.g., BA, 2-EHA) lowers Tg and enhances chain mobility. Blending with high-Tg monomers (e.g., MMA) in controlled ratios balances tack with strength.
Plasticizers: Adding low-molecular-weight esters or oils reduces viscosity, improving wetting and tack. However, over-plasticization can cause migration, diminishing long-term performance.
Tackifiers: Hydrocarbon or rosin-based tackifiers increase surface stickiness by reducing the resin’s glass transition temperature and enhancing surface energy. They are particularly effective in pressure-sensitive acrylic adhesives.
4. Adhesion: Substrate Bonding and Mechanisms
Adhesion refers to the long-term bond strength between the acrylic resin and a substrate, critical for durability in applications like coatings, adhesives, and laminates. It depends on chemical, physical, and mechanical interactions at the resin-substrate interface.
4.1 Adhesion Mechanisms
Acrylic resins achieve adhesion through multiple mechanisms, often acting in concert:
Chemical Bonding: Polar functional groups (e.g., carboxyl, hydroxyl) in the resin react with substrate surfaces (e.g., metal oxides, hydroxyl groups on wood or glass), forming covalent or ionic bonds. For example, acrylic acid-containing resins bond strongly to metals via carboxylate formation.
Mechanical Interlocking: The resin penetrates microscopic pores or irregularities in rough substrates (e.g., concrete, fabric), creating a "mechanical anchor" when cured.
Dispersive Forces: Van der Waals interactions between the resin and substrate dominate for non-polar substrates (e.g., polyolefins), requiring resin formulation with low-polarity monomers to match surface energy.
Diffusion Bonding: For polymer substrates (e.g., PVC, PET), resin chains may diffuse into the substrate’s surface, forming an interpenetrating network that enhances adhesion.
4.2 Factors Influencing Adhesion
Substrate Properties: Surface roughness, polarity, and cleanliness significantly impact adhesion. Polar substrates (e.g., metals, ceramics) bond more readily to acrylic resins with polar functional groups, while non-polar substrates (e.g., polyethylene) require surface treatment (e.g., corona discharge) or resin modification with adhesion promoters.
Resin Formulation: Incorporating polar monomers (e.g., acrylic acid, hydroxyethyl acrylate) enhances interactions with polar substrates. Cross-linking improves adhesion durability by reducing polymer chain mobility and resisting environmental factors (e.g., moisture, heat).
Environmental Conditions: Humidity, temperature, and chemical exposure can degrade adhesion. Acrylic resins with high cross-link density or hydrophobic monomers (e.g., isobornyl acrylate) exhibit better moisture resistance, preserving adhesion in wet environments.
5. Strength: Cohesive Integrity and Mechanical Performance
Strength in acrylic resins refers to their ability to resist deformation or fracture under stress, encompassing tensile strength, shear strength, and elongation at break. It is primarily a function of the resin’s molecular structure and network architecture.
5.1 Mechanisms of Strength
Molecular Weight: Higher molecular weights increase chain entanglement, enhancing tensile and shear strength. For example, acrylic resins with molecular weights exceeding 500,000 g/mol exhibit superior cohesive strength compared to low-molecular-weight counterparts.
Cross-Linking: Covalent cross-links between polymer chains create a three-dimensional network, improving modulus and strength. The degree of cross-linking is critical: cross-linking enhances strength without brittleness, while excessive cross-linking reduces flexibility and may cause cracking under stress.
Crystallinity: Semicrystalline acrylic resins (e.g., those incorporating methacrylate esters with long alkyl chains) exhibit higher strength due to ordered crystalline domains, which act as physical cross-links.
5.2 Balancing Strength with Other Properties
Strength often trades off with tack and flexibility. For example:
Structural adhesives require high strength and adhesion, achieved via high cross-link density and polar monomers, but this reduces tack.
Pressure-sensitive adhesives prioritize tack and moderate adhesion, using low cross-linking and flexible monomers, with strength limited to prevent substrate damage during removal.
Formulation strategies to balance these properties include:
Core-Shell Polymerization: Creating particles with a soft, tacky core and a hard, strong shell allows independent tuning of tack and strength.
Gradient Copolymers: Designing resins with monomer gradients (e.g., polar to non-polar) optimizes adhesion at the substrate interface while maintaining strength in the bulk.
6. Testing and Characterization Methods
Accurate measurement of tack, adhesion, and strength is essential for quality control and formulation optimization. Industry-standard methods include:
Tack Testing:
Loop Tack Test: Measures the force required to separate a resin-coated loop from a substrate, quantifying immediate stickiness.
Probe Tack Test: Uses a spherical probe to assess the resin’s ability to adhere under controlled contact time and pressure.
Adhesion Testing:
Peel Adhesion Test: Determines the force needed to peel a resin-coated tape from a substrate at a specified angle (e.g., 90° or 180°).
Shear Adhesion Failure Temperature (SAFT): Evaluates adhesion durability under elevated temperatures and constant shear stress.
Strength Testing:
Tensile Strength Test: Measures the maximum stress a resin can withstand before breaking, typically using ASTM D638 standards.
Shear Strength Test: Determines resistance to parallel forces, critical for structural adhesives (ASTM D1002).
Advanced techniques like atomic force microscopy (AFM) and X-ray photoelectron spectroscopy (XPS) provide insights into interfacial interactions, while dynamic mechanical analysis (DMA) characterizes viscoelastic behavior, linking structure to performance.
7. Applications and Technological Innovations
Acrylic resins, tailored for specific tack, adhesion, and strength profiles, find applications across industries:
Pressure-Sensitive Adhesives (PSAs): Used in tapes, labels, and medical dressings, these require high tack, moderate adhesion, and low to moderate strength for clean removability. Formulations often include 2-EHA, tackifiers, and minimal cross-linking.
Structural Adhesives: Employed in automotive and aerospace bonding, these demand high adhesion and strength, achieved via cross-linked acrylics with polar monomers (e.g., hydroxyethyl methacrylate).
Coatings: Architectural and automotive coatings balance adhesion to substrates, strength to resist abrasion, and minimal tack for a smooth finish, using cross-linked acrylics with MMA and weather-resistant monomers.
Medical Devices: Biocompatible acrylics in wound care products require gentle tack, strong adhesion to skin, and strength to withstand movement without delamination.
Recent innovations include:
Stimuli-Responsive Acrylics: Resins that adjust tack or strength in response to temperature, pH, or light, enabling on-demand bonding and debonding.
Bio-Based Acrylics: Monomers derived from renewable sources (e.g., lactic acid-based acrylates) offer sustainable alternatives with comparable tack, adhesion, and strength.
Nanocomposite Acrylics: Incorporating nanoparticles (e.g., silica, clay) enhances strength and adhesion without sacrificing tack, ideal for high-performance coatings and adhesives.
8. Conclusion and Future Outlook
Acrylic resins technology continues to advance, driven by the need to precisely tune tack, adhesion, and strength for diverse applications. The ability to manipulate monomer composition, molecular weight, cross-linking, and additive incorporation allows unprecedented control over these properties, enabling solutions for everything from disposable tapes to high-strength structural bonds.
Future trends will focus on sustainability, with bio-based monomers and recyclable formulations reducing environmental impact. Additionally, smart acrylic resins—with self-healing capabilities or adaptive tack/adhesion—will address emerging needs in robotics, wearable technology, and advanced manufacturing. As our understanding of structure-property relationships deepens, acrylic resins are poised to remain at the forefront of adhesive and coating innovation, offering versatile, high-performance solutions for evolving industrial challenges.
References
[1] Brown, R. J., & Smith, L. M. (2021). Tack, adhesion, and cohesion in acrylic pressure-sensitive adhesives. Journal of Adhesion Science and Technology, 35(12), 1345-1368.
[2] Garcia, M. A., et al. (2020). Molecular design of acrylic resins for enhanced adhesion to low-surface-energy substrates. Polymer Chemistry, 11(5), 923-935.
[3] ASTM International. (2019). Standard Test Methods for Pressure-Sensitive Adhesives (ASTM D3359). West Conshohocken, PA: ASTM.
[4] Liu, Y., et al. (2022). Sustainable acrylic resins: From bio-based monomers to tunable tack and strength. Green Chemistry, 24(8), 3210-3225.