1. Introduction
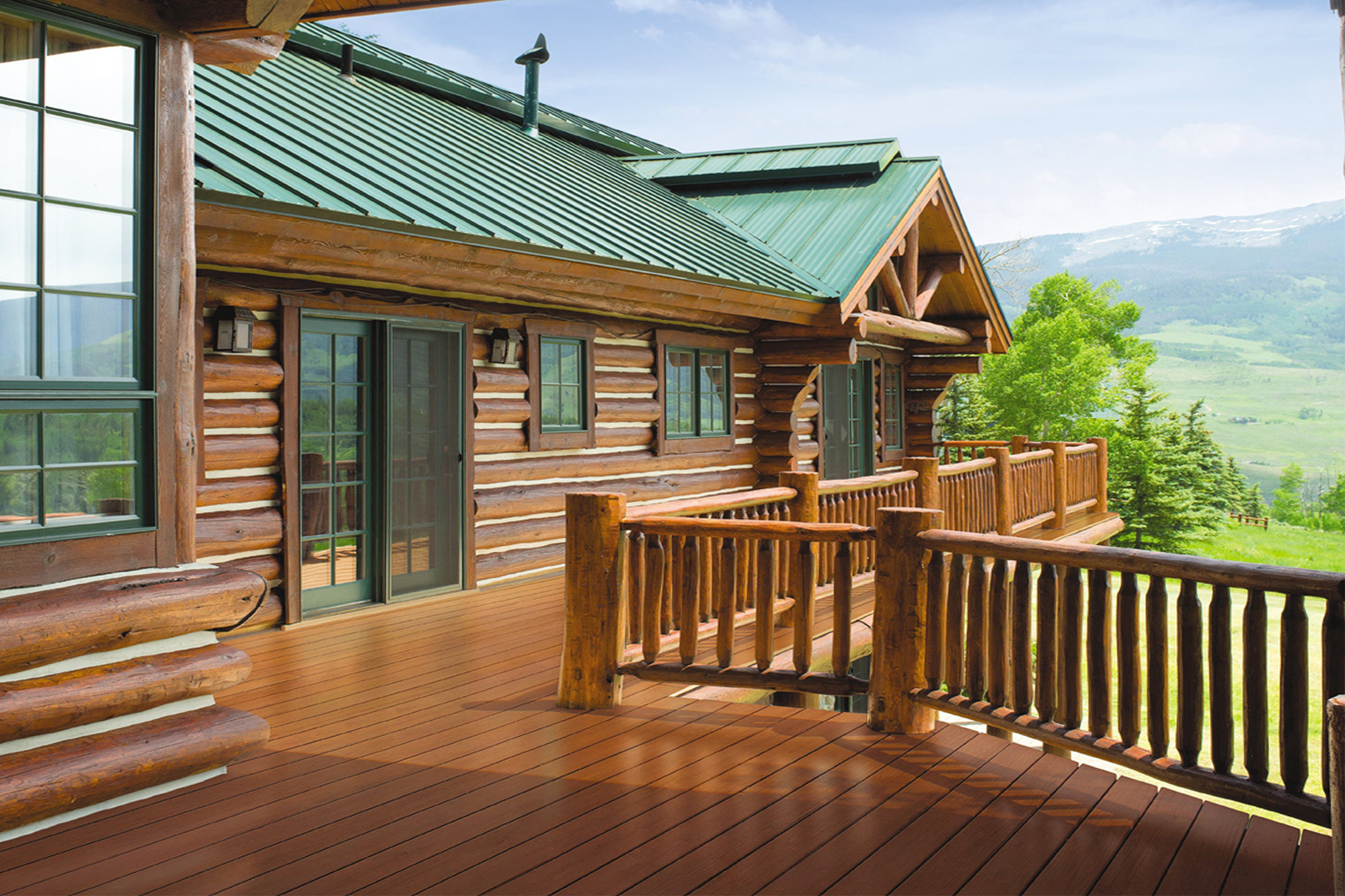
The automotive industry places stringent demands on surface finishes, which must not only deliver a pristine, high-gloss appearance but also withstand harsh environmental conditions, mechanical impacts, and everyday wear. Among the various forms of surface damage, scratches—caused by debris, washing, or accidental contact—are a primary concern, as they compromise aesthetics and can accelerate corrosion. Traditional automotive coatings, while offering basic protection, often struggle to balance scratch resistance with other critical properties such as flexibility, weatherability, and ease of application.
Acrylic resins have long been valued in automotive coatings for their excellent weatherability, UV resistance, and optical clarity. However, pure acrylic resins lack the inherent hardness and scratch resistance required for modern automotive standards. To address this limitation, acrylic resin composites—incorporating reinforcing fillers, nanoparticles, or functional additives—have been developed. These composites leverage the synergistic effects between acrylic matrices and reinforcing agents to enhance scratch resistance while preserving or improving other key properties. This article provides a comprehensive overview of acrylic resin composites for scratch-resistant automotive finishes, exploring their composition, performance mechanisms, and practical applications.
2. Fundamentals of Acrylic Resins in Automotive Coatings
Acrylic resins used in automotive finishes are typically copolymers synthesized from monomers such as methyl methacrylate (MMA), butyl acrylate (BA), and 2-ethylhexyl acrylate (EHA). Their chemical structure, characterized by a saturated carbon backbone and pendant ester groups, endows them with several advantageous properties:
Weatherability: The saturated backbone resists oxidation and UV-induced degradation, ensuring long-term color stability and gloss retention.
Optical Clarity: Amorphous acrylic resins exhibit high transparency, critical for achieving a deep, reflective finish.
Adhesion: They adhere well to various substrates, including metal, plastic, and precoated surfaces, forming durable bonds.
Customizability: By adjusting monomer ratios, properties like glass transition temperature (Tg), flexibility, and cross-linking density can be tailored to meet specific coating requirements.
In automotive applications, acrylic resins are often cross-linked with melamine-formaldehyde or isocyanate hardeners to form thermoset networks, enhancing chemical resistance and hardness. However, even cross-linked acrylics face challenges in scratch resistance, as their relatively low surface hardness makes them susceptible to micro-scratches and marring. This limitation has driven the development of composite systems that integrate reinforcing agents.
3. Reinforcing Agents for Scratch Resistance
The incorporation of reinforcing agents into acrylic resin matrices is the primary strategy for enhancing scratch resistance. These agents act through mechanisms such as increasing surface hardness, promoting energy dissipation during impact, or preventing crack propagation. Key types of reinforcing agents include:
3.1 Nanoparticles
Nanoparticles, with dimensions typically ranging from 1 to 100 nm, are widely used in acrylic composites due to their high surface area-to-volume ratio, which enables strong interfacial interactions with the polymer matrix. Common nanoparticles include:
Silica (SiO₂): Fumed or colloidal silica nanoparticles are among the most prevalent, as they form strong covalent bonds with acrylic resins (via silane coupling agents), increasing hardness and scratch resistance. Their spherical shape minimizes light scattering, preserving optical clarity.
Alumina (Al₂O₃): Alumina nanoparticles enhance both hardness and abrasion resistance, making them suitable for high-wear areas. However, their higher refractive index requires careful dispersion to avoid haze.
Zirconia (ZrO₂): Zirconia nanoparticles offer a balance of hardness and toughness, reducing brittleness often associated with highly filled composites.
Carbon Nanotubes (CNTs) and Graphene: These carbon-based nanoparticles improve not only scratch resistance but also electrical conductivity (useful for anti-static coatings) and thermal stability, though their high cost limits widespread adoption.
The effectiveness of nanoparticles depends on uniform dispersion; agglomeration can lead to stress concentration and reduced performance. Surface modification with coupling agents (e.g., silanes, titanates) is critical to improving compatibility with the acrylic matrix.
3.2 Microscale Fillers
Microscale fillers, such as glass flakes, mica, or ceramic microspheres, are used to enhance scratch resistance through different mechanisms:
Glass Flakes: Thin, flat glass flakes create a barrier effect, increasing surface hardness and reducing the depth of scratch penetration. They also improve corrosion resistance by blocking moisture and chemical ingress.
Ceramic Microspheres: Hollow or solid ceramic microspheres distribute stress during impact, reducing the likelihood of scratch formation. They are particularly useful for balancing weight and performance in lightweight automotive components.
While microscale fillers can enhance scratch resistance, they may compromise optical clarity if not properly dispersed, making them more suitable for non-gloss or textured finishes.
3.3 Functional Additives
In addition to particulate fillers, functional additives play a role in optimizing scratch resistance:
Lubricants: Additives like polytetrafluoroethylene (PTFE) or silicone oils reduce friction between the coating surface and abrasive particles, minimizing scratch initiation.
Cross-Linking Agents: Advanced cross-linkers (e.g., blocked isocyanates, epoxy resins) increase the density of the polymer network, enhancing surface hardness without excessive brittleness.
Photostabilizers: UV absorbers and hindered amine light stabilizers (HALS) prevent UV-induced degradation of both the acrylic matrix and reinforcing agents, maintaining scratch resistance over time.
4. Mechanisms of Scratch Resistance in Acrylic Composites
Scratch resistance in acrylic resin composites is governed by a combination of mechanical and surface properties, with reinforcing agents contributing through several key mechanisms:
Hardness Enhancement: Nanoparticles and microfillers increase the composite’s surface hardness, reducing the likelihood of plastic deformation or indentation from abrasive particles. For example, silica nanoparticles form a rigid network within the acrylic matrix, resisting penetration by sharp objects.
Toughness Improvement: Reinforcing agents like zirconia or rubber-modified particles absorb energy during impact, preventing crack propagation. This is critical for avoiding catastrophic failure when the coating is subjected to larger scratches.
Reduced Friction: Lubricating additives lower the coefficient of friction, minimizing the force required to move abrasive particles across the surface and reducing scratch depth.
Interfacial Bonding: Strong adhesion between the acrylic matrix and reinforcing agents ensures efficient stress transfer, preventing filler detachment during scratching—detached particles can act as abrasives themselves, exacerbating damage.
The optimal balance of hardness and toughness is crucial; overly hard composites may be brittle, leading to cracking under impact, while overly flexible systems may exhibit poor scratch resistance.
5. Formulation and Manufacturing Considerations
Developing effective acrylic resin composites for automotive finishes requires careful formulation and processing to ensure uniform dispersion of reinforcing agents, optimal curing, and consistent performance:
Dispersion Techniques: High-shear mixing, ultrasonic processing, and ball milling are used to disperse nanoparticles evenly in the acrylic matrix, preventing agglomeration. In situ polymerization—where monomers are polymerized in the presence of pre-dispersed nanoparticles—can also enhance dispersion by promoting chemical interactions between the matrix and fillers.
Curing Conditions: Thermoset acrylic composites require precise control of curing temperature and time to achieve full cross-linking. Over-curing may lead to brittleness, while under-curing reduces hardness and chemical resistance.
Coating Application: These composites are typically applied via spray coating, electrostatic deposition, or dip coating. The application method affects film thickness uniformity, which in turn influences scratch resistance—thicker films may offer more protection but can suffer from poor adhesion or cracking.
Compatibility Testing: Reinforcing agents must be compatible with other coating components, such as pigments, solvents, and catalysts, to avoid issues like sedimentation, viscosity changes, or loss of optical properties.
6. Performance Evaluation of Scratch-Resistant Composites
The performance of acrylic resin composites in automotive finishes is evaluated using industry-standard tests to assess scratch resistance and related properties:
Taber Abrasion Test: Measures weight loss or gloss retention after repeated abrasion with standardized wheels, providing a quantitative assessment of resistance to wear.
Pencil Hardness Test: Determines the hardest pencil grade that does not scratch the coating, indicating surface hardness.
Cross-Cut Adhesion Test: Evaluates adhesion to the substrate, ensuring the coating does not delaminate under stress.
Weathering Tests: Accelerated UV exposure and humidity cycling assess long-term stability, ensuring scratch resistance is maintained over time.
Gloss Measurement: Specular gloss at 20°, 60°, and 85° angles is measured before and after scratching to evaluate aesthetic impact.
Advanced techniques like atomic force microscopy (AFM) and scanning electron microscopy (SEM) are also used to analyze scratch morphology, providing insights into damage mechanisms at the microscale.
7. Applications and Industry Trends
Acrylic resin composites for scratch-resistant finishes are used across various automotive components, including:
Exterior Surfaces: Body panels, bumpers, and mirrors benefit from enhanced resistance to road debris and washing-induced scratches.
Interior Components: Dashboard trim, door handles, and center consoles require scratch resistance to withstand daily use.
Plastic Parts: Lightweight plastic components (e.g., polycarbonate headlamp covers) use these composites to maintain clarity and resist scratching.
Current trends in the industry include:
Sustainability: Development of bio-based acrylic resins and renewable reinforcing agents (e.g., cellulose nanocrystals) to reduce environmental impact.
Self-Healing Composites: Integration of microcapsules containing healing agents that rupture upon scratching, releasing materials to repair damage.
Multifunctional Coatings: Combining scratch resistance with other properties like anti-fingerprint, anti-fog, or thermal management capabilities.
8. Conclusion and Future Outlook
Acrylic resin composites have proven to be highly effective for scratch-resistant automotive finishes, offering a compelling balance of optical clarity, weatherability, and mechanical performance. By incorporating nanoparticles, microfillers, and functional additives, these composites address the limitations of pure acrylic resins, meeting the demanding requirements of modern automotive applications.
Future research will focus on refining dispersion techniques to enhance the performance of nanocomposites, developing self-healing mechanisms to extend coating lifespan, and reducing reliance on non-renewable materials. As consumer expectations for vehicle durability and aesthetics continue to rise, acrylic resin composites are poised to play an increasingly central role in the next generation of automotive coatings, driving innovation in both formulation and application.
References
[1] Chen, L., & Wang, H. (2021). Nanoparticle-reinforced acrylic composites for automotive scratch-resistant coatings. Progress in Organic Coatings, 156, 106324.
[2] Miller, A. J., et al. (2020). Scratch resistance mechanisms in acrylic-silica nanocomposites. Journal of Coatings Technology and Research, 17(4), 987-1001.
[3] Automotive Industry Action Group (AIAG). (2019). Standard Test Methods for Evaluation of Automotive Coatings. Southfield, MI: AIAG.
[4] Zhang, Q., et al. (2022). Sustainable acrylic composites with cellulose nanocrystals for scratch-resistant finishes. Green Chemistry, 24(3), 1123-1135.